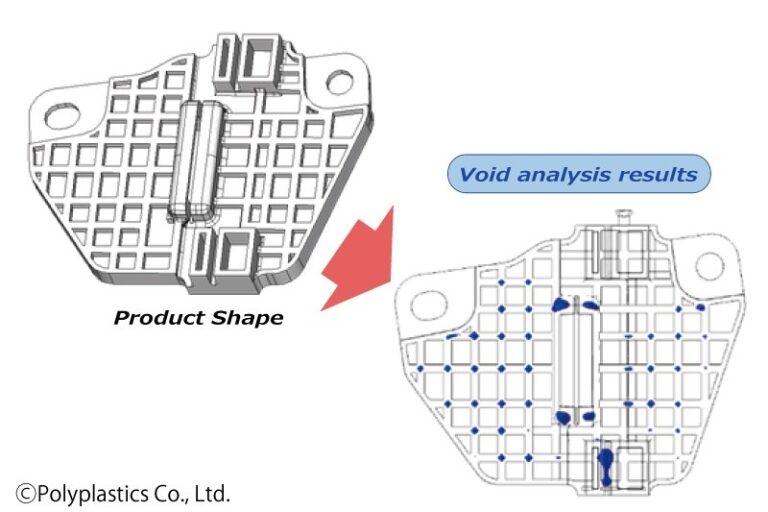
Engineering thermoplastics supplier Polyplastics Co. Ltd. has developed a CAE analysis technology that predicts the occurrence of voids in injection molded products made from its Duracon POM. By predicting the risk of voids before creating the mold, Polyplastics says this CAE tool can shorten the development cycle and avoid costly mold changes after the tool is built.
Polyplastics void-prediction technology considers changes in process variables including temperature and pressure during the resin solidification process. The program verifies the shape, molding conditions and effects of changes in the gate position, while also displaying the size and location of the voids.
Voids can form near the center of thick injection molded products, and in the past, parameters like volume shrinkage predicted by flow analyses had been used for void prediction, but Polyplastics says the accuracy of this method has been questioned since the actual phenomenon can’t be recreated.
By contrast, Polyplastics’ new void prediction technology links flow analysis via Moldflow with structural analysis via ADVENTURECluster to predict the formation of voids according to strain arising inside molded products. To do so it takes into consideration mold shrinkage, elastic modulus and pressure distribution during resin solidification.
Read: Strong Growth for High-Sliding Polyacetal Grades for Gears, Bearings
For the pictured part, measuring 102 mm wide by 130 mm long, Polyplastics undertook a validity evaluation for the void prediction technology, modeling off Duracon POM M90-44. CT scans of parts molded with a tool temperature of 40, 80 and 120°C were used for particle and pore analysis and then compared to the void analysis results, which Polyplastics said showed a “highly accurate prediction of where voids occurred.”
Polyplastics is offering the new technology as part of its overall technical support for current POM customers.
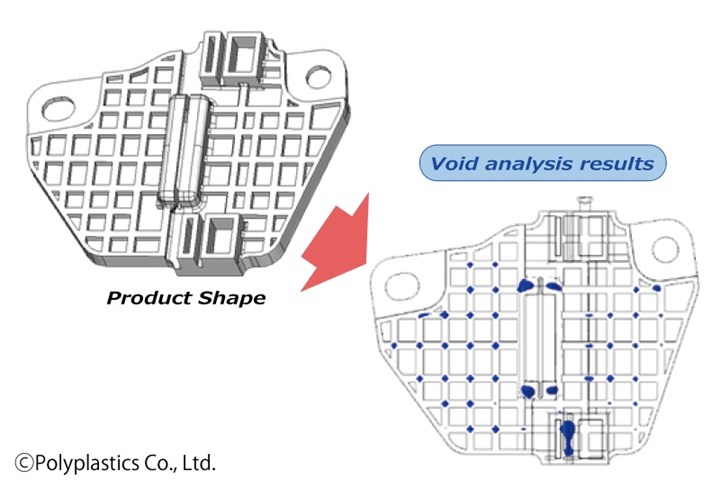
Polyplastics’ void prediction technology predicts the formation of voids according to resin flow, temperature, pressure, and structural analyses, which show strain distribution.
Photo Credit: Polyplastics