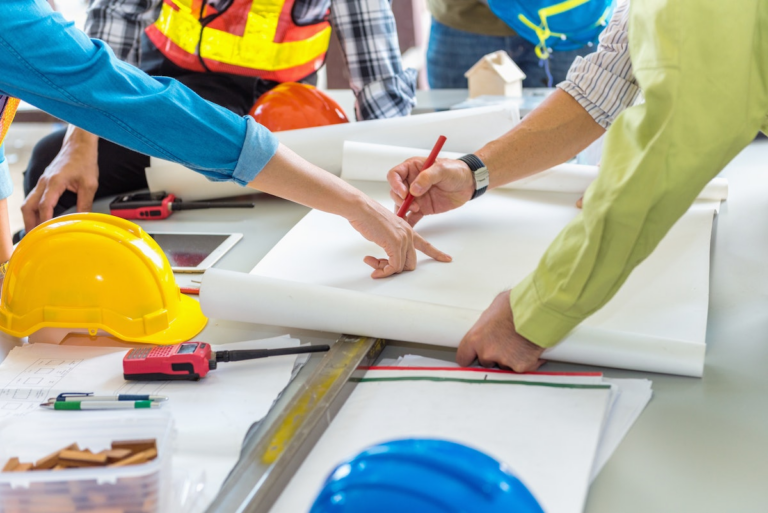
Whenever a construction company bids for a project, they give not just a price breakdown, but also provide an indication of how quickly they’ll be able to get the job done. Once contracts are signed, though, those promises collide with reality — and projects start to get delayed.
Nine out of 10 contractors say they see frequent construction delays, according to research reports. On average, 72% of all construction projects wind up running late, and affected projects see their total duration overrun by an average of 38%, driving up project costs by an average of 24%.
Some delays are inevitable, of course. But there’s a risk of construction professionals beginning to grow resigned to delays, and failing to take action to ensure productivity and efficiency on their worksites. The problem can become self-fulfilling: because we expect delays, we stop trying to prevent them.
In an industry where business failure rates run remarkably high, this is a problem that urgently needs solving. The reality is that construction delays aren’t a law of nature, and we aren’t powerless to prevent (or at least minimize) their impact on our projects and our customers.
Below are 5 ways to keep your projects running on time.
1. Set Realistic Expectations
In many cases, supply chain disruptions have made it impossible to complete projects as quickly as planned: some companies have seen lead times for structural steel balloon from 12 weeks to 30 weeks or more, for instance. Roofing insulation and other critical products are also hard to obtain, forcing workers to sit idle until deliveries are made.
Make sure everyone on your team has visibility into these kinds of bottlenecks so you can give quotes that reflect the reality of the environment you’re operating in, and so you can quickly update your customers if matters beyond your control look set to cause delays. Everyone knows some delays can’t be avoided, so set realistic expectations and be proactive about letting everyone know if problems arise.
2. Use Your Team Effectively
Almost 50% of time is wasted on job sites — and even if some delays are unavoidable, that kind of non-productivity is preventable. Construction companies need clear systems in place to ensure workers aren’t sitting idle: if a team can’t complete one task due to labor or material shortages, site managers should be able to flexibly reassign them to other work, or even other job sites.
The reality is that when workers are idling, it’s usually their supervisors who bear the responsibility. Make sure your team leaders have the resources and knowledge they need to make smart decisions in real time, and maximize productivity for the people they’re managing.
3. Embrace Checklists
Checklists might not sound like a transformative technology — but for many construction companies, they’re a real gamechanger. The key is to look beyond clipboards and crumpled bits of paper, and embrace digital tech that lets stakeholders from across the entire project ecosystem access and update checklists from tablets or smartphones.
Digital lists are less likely to be overlooked by frontline workers, and they also make it possible for project supervisors to have full visibility into what’s getting done. With the right checklists, you can empower workers to manage their own time, while still making sure everyone stays on track.
4. Keep on Communicating
Often, delays and requests for rework happen because key stakeholders don’t communicate properly. Project managers and site staff should hold regular stand-up meetings to track progress and preempt potential problems, of course. Messaging tools also can help your teams to seek help or advice without disrupting their work, use photos and videos to highlight specific queries or examples, or access blueprints and other information in the moment that it’s needed.
If you’re working across multiple job sites, digital tech can also help managers and teams stay connected, boosting productivity across the board and helping to ensure quality control processes are adhered to.
5. Don’t Forget About Data
Modern worksites are increasingly driven by data, so it’s important to ensure you’re putting systems in place to manage and keep track of the information flowing through your work processes. Data needs to be a force multiplier, not a source of confusion and potential delays.
Make sure your teams have the data they need at their fingertips, using mobile devices or tablets to access plans and information on an as-needed basis. Ideally, use a single connected back-end platform to manage data across your head office and all worksites, keeping managers and jobsite teams on the same page at all times.
Don’t Settle for Second-rate
The bottom line is that yes, construction is a complex business, and yes, delays are inevitable. But in an industry where so many operators are growing complacent, and treating lengthy delays as simply the way things are done, there’s a real opportunity for contractors that prioritize organizational efficiency to stand out from the pack.
That starts with refusing to accept that delays are simply a law of nature when it comes to construction projects. New digital innovations are making it possible to drive efficiencies across the value chain for construction projects of all kinds and sizes — and that, in turn, is making the construction industry a better-organized and more professional place for everyone.
In a world of disruptions, labor shortages, and supply chain issues, you can’t control everything. But that’s all the more reason to take control of the things you do have the power to influence, and to ensure that you aren’t exacerbating inevitable hiccups by allowing preventable missteps to derail your projects.
So don’t resign yourself to long, revenue-sapping delays. With the right technologies, smart processes, and well-trained and motivated workers and managers, it’s possible to keep your projects running on schedule — and to delight your customers and boost your revenues in the process.