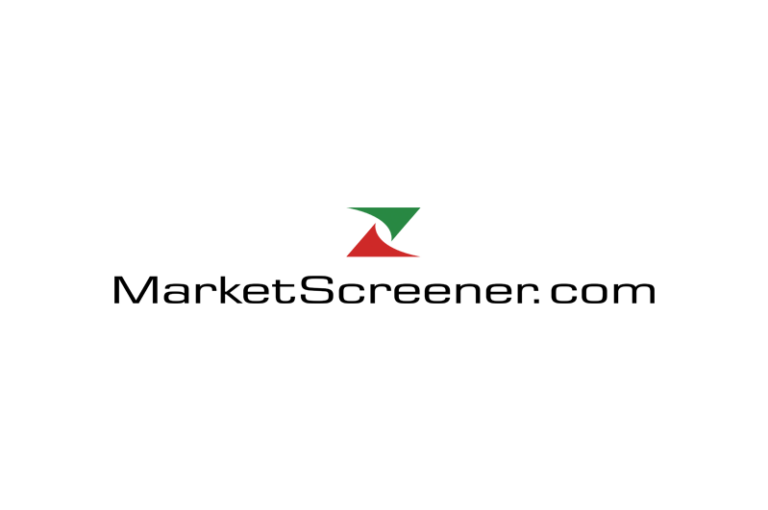
12/01/2022
“Help, I’m building a wooden skyscraper!” This or something similar might be what some new builders are thinking these days. The race for the tallest wooden house has been on for a long time, and one prestigious building follows another all over the world. Without extensive preliminary planning, such a project will not succeed. Our timber construction team gives practical tips for project management.
Hoch, höher, am höchsten: Das Bauen mit Holz ist derzeit sehr attraktiv. Zunehmend spielt der Mehrgeschossbau eine Rolle. Doch auf dem Weg zum erfolgreich absolvierten Bau-Projekt lauern viele Stolpersteine.
An article by Peter Hartmann (SCHULER Consulting) and Michael Postulart (SCHULER Consulting). Published in möbelfertigung, issue 07/2022.
What makes the ‘timber construction business’ popular and how to become successful in it
The race is on: One prestigious project follows the next. The current tallest timber building, “Mjøstårnet” (Brumunddal, Norway), at 85.4 metres, must soon surrender its place to the next record chaser, the “Rocket” in Winterthur, which is scheduled to reach the 100-metre mark in 2026. With timber construction, many want to reach high. Multi-storey buildings are often intended not only to set new construction standards, but also to serve as an example of urban living. The wooden giants are unique, but they have one thing in common: projects of this kind are complex. From vision to implementation, there are several hurdles to overcome. Schuler Consulting helps companies navigate through the jungle of project requirements and implement construction projects efficiently and strategically from design to production. Timber construction engineer Peter Hartmann and wood technology engineer Michael Postulart report on what makes the timber construction business popular and how to become successful in it.
Out of the niche, into the market
The future lies in timber construction. Many entrepreneurs have recognised this. Both investors who come from the classical object construction with mineral building materials as well as non-industry stakeholders are looking for their place in the market. Those who build on wood now are moving with the trend, for timber construction offers answers to modern man’s question of sustainable and affordable living space. By 2050, more than two billion additional individuals are expected to be seeking a roof over their heads. Consequently, when it comes to the housing industry to cope with this major task, wood can literally go the extra mile: In housing densification, wood as a building material is already superior to other materials due to its special material properties (low weight, high stability).
But it is not only the building material itself that is appealing: strengthened by political offensives and the social demand for “green building”, timber construction is developing out of its niche into a real movement. Wood is also a showcase candidate in terms of climate friendliness: while conventional construction emits up to 600 kg of CO2 per tonne of cement, the wood used in multi-storey buildings in timber construction saves more CO2 than is emitted during the construction project. In the case of hybrid construction methods, i.e. a combination of elements made of wood and wood-based materials as well as elements made of e.g. concrete, it is the ratio that counts – every component that is not made of concrete saves CO2 emissions. For example, a single-family house binds about 40 tonnes of CO2and requires only half as much CO2 in production as a concrete building. This already makes timber construction attractive today, but especially in the long term, also from a business perspective, since lower CO2 emissions consequently mean less CO2 tax.
“The possibilities of timber construction are being expanded step by step. Even bigger, even higher or even more sustainable – there are always new benchmarks. Building with wood is very attractive for many: for residents, for politicians – who must also set new framework conditions in the building sector in order to comply with the agreed climate agreements – and not least for economic reasons. However, in timber construction, which has not been a “pioneer sector” for a long time, there have so far been few standards to fall back on when implementing such complex projects as multi-storey buildings or housing developments,” reports Michael Postulart. On the one hand, this makes the market attractive, as there is a lot of design scope for architects, investors and engineers, Postulart continues. “It invites you to think big and, of course, to build high.” On the other hand, due to their complexity, projects in multi-storey construction place high demands on project management and project execution.
Schuler Consulting says this is noticeable, among other things, in the fact that companies from the timber construction sector are increasingly looking for strategic advice. “Our task as project engineers is then to look for lean ways in the project to implement the visions of the timber constructors economically and efficiently,” confirms Peter Hartmann. To approach the question of how to become successful in timber construction, especially in large-scale projects, the two share a few practical tips from their own experience.
7 tips for successful project management in multi-storey construction
1. Know your product
Every project starts with an idea, which can quickly grow in complexity. It is important to define the building project clearly from the beginning. This means, firstly, knowing your product and what you want to get out of it at the end of the project and, secondly, making a detailed business case. A business case is necessary to make one’s vision economically tangible and to place it on a firm foundation that will withstand all risk assessments in the best case scenario. “At the beginning of the project there is always the question of the product – what is to be built, how high, what is the vision in terms of sustainability and economic viability and much more. Then there is a risk assessment by the project management. These are many questions that have to be clarified at the beginning in order to start the project cleanly,” explains Senior Consultant Peter Hartmann.
2. Know your stakeholders
At the beginning, it is necessary to have a view of the whole and not to lose it during the entire course of the project. This means knowing the requirements of all the people involved, such as architects, the building physicists and technical building planners, logisticians and buyers. Each of them brings a large catalogue of requirements and wishes that need to be sorted, structured and prioritised. Often, classic conflicting goals between the different technical planners – fire protection, sound insulation, thermal insulation, statics, building services, architecture – have to be coordinated and aligned with the project goal. Also new on board here is the production planner, who wants a product that can be manufactured as highly automated as possible to an economically feasible extent. “As project managers, we play a kind of conductor in a construction and factory planning project, bringing together or ‘orchestrating’ the concerns of the different planners in such a way that the end result is a product that can be produced smartly,” Hartmann continues.
3. Small changes, big impact
Furthermore, team size is crucial for successful project management. While small teams create a fast and agile working environment that also delivers results and implements changes at short notice, large teams bring the necessary “manpower” to check changes down to the last detail. Even small changes in the construction have a great radiance in other areas: If the thickness of the timber frame construction is changed, this has an impact on the statics. If another layer is added to the wall structure, e.g. to improve the physical properties of the building, the additional work steps and thus the entire cycle time in the coordinated prefabrication must be adjusted. Such changes also have a further impact on fire and noise protection, as well as thermal insulation, for example if the dew point slips into an unfavourable range as a result of the change.
In large teams, there are enough specialist planners who can produce fully comprehensive designs for this. The challenge is to keep the threads in hand and bring them together properly. “The more players there are in the game, the more views and opinions from different disciplines come up. This brings opportunities and risks. The project manager’s task is to choose the right path, to develop the most target-oriented idea and to take the entire team along with him on this path,” says Michael Postulart.
4. What do you think about logistics?
The crucial question in all projects is logistics. It is often easier to manufacture the timber elements in the production environment than to then transport the elements to the construction site using an economically interesting transport process. The larger the projects, the greater the advantages of sophisticated logistics. Thus, a marginal topic that is inconspicuous at the beginning often gains a lot of attention in the projects. One of the reasons for this is that logistics is one of the major cost drivers in the value chain. With the progressive increase in CO2 taxation and the associated rise in transport costs, the pressure for optimised logistics is growing. Particularly large production volumes result in a high number of loading cycles, which require smart and often individual loading concepts. Here Schuler develops concepts tailored to the customer with the surrounding logistics in the production and warehouse environment.
5. Certificates don’t just hang on the wall
The issue of sustainability is becoming increasingly important in construction projects. Many large insurance companies, funds and investors attach importance to building certification. Through certification, builders and investors hope for greater competitiveness in the real estate market and higher returns over the entire life cycle of the property. Over the last decades, various national as well as international methods and models have developed (DGNB, LEED, BREEAM, etc.). What do these topics have to do with factory planning? Depending on the model, the manufacturing process of the building elements flows into the certification with different weighting, i.e. CO2 emissions, waste, transports, etc. are a direct lever that has a positive or negative effect on the certification, depending on the process and construction design,” explains Hartmann.
Another and often decisive point is the element construction, the timber engineer continues. “The certification goals are linked to various point systems that have a very practical effect on the element construction. For example, which fasteners are used and how well they enable recycling, or what the energy requirements of the property are, i.e. how good the combination of thermal insulation and building services must be. These issues have a direct influence on the production and assembly processes.” For this reason, it is important to have made the basic decisions at the beginning of the planning process (see Tip 1). What is my vision? How sustainable do I want to be? Which certification do I strive for and with which goal achievement? “Who” is in the lead – efficiency/cost, producibility, sustainability or design? All these issues are considered in the roadmap of a planning project.
6. Raise the automation level!
In addition to the sustainability goals and the construction details of the elements, other guard rails are important in the project. At the beginning, it should be defined what the degree of prefabrication and automation should be in the later production. The great timber construction boom is also due to the possibilities of automation and a higher degree of prefabrication. But a mere shift of value creation from the construction site to the production hall is no longer sufficient, skilled workers are also very difficult to recruit in an orderly industrial environment on the production floor. Since this problem will not be alleviated and the general trend is towards automation anyway, a high degree of automation should be aimed for here. This increases the complexity of the project, but with the right product and efficient and automated production, there is the possibility of successfully creating housing in the future with planning certainty, despite challenges such as the shortage of skilled workers and the energy crisis.
7. Know the developments in the market
The timber construction market is dynamic, so it is particularly important to observe current developments and to be aware of innovations, e.g. in the area of certifications, in good time. Risks and opportunities must be derived from what is happening in the market and their effects on the project must be assessed. For example, a look into the distant future offers hope that rising construction costs will reduce the requirements for building, especially in the area of affordable housing. Currently, the requirements are still very high, but a change must take place here in perspective. A stronger consideration of timber construction in the standards compared to conventional construction would also create relief in fire and noise protection. Optimisations in these areas could further increase the attractiveness of building with wood by simplifying the constructions and thus creating a further step towards affordable housing. Current risks for timber construction projects, on the other hand, are the currently long delivery times of machinery suppliers. The machine manufacturers are working to capacity and with a procurement crisis for raw materials and many machine components, which means that longer delivery times should be planned for in the business case, especially for larger plants.
Conclusion
“Strategic production development often looks frighteningly complex at the outset, taking into account all stakeholders, constraints and regulations,” Peter Hartmann summarises. “However, when considering the long life cycle of real estate or processes in the construction industry, it becomes clear that holistic planning is necessary in order to be able to produce sustainably and efficiently. In the end, the aim is to deliver sustainable and affordable housing to the end customer with increased efficiency and profitability, and thus to operate successfully in the market.” Those who want to take off in timber construction therefore set the course for success through strategic and efficient project management. And that is necessary, because: There is a lot going on in the industry!
The constant race to build the next tallest wooden skyscraper shows how competitive the market is. According to Michael Postulart, timber construction will continue to gain significant shares in the coming years. “In my opinion, the timber construction boom will continue, even if the general construction boom, especially for single-family houses, is currently declining somewhat. Timber construction will hopefully quickly replace classic construction with concrete and the very CO2-intensive cement production as the predominant construction method.” It will not be possible to do without cement and concrete completely, says the engineer for wood technology. “In doing so, we should limit ourselves to the sensible components, as the hybrid construction method demonstrates.”
The engineers agree: the “timber construction business” is and will remain popular. In order to be successful in it, Schuler Consulting offers support for everyone – whether the project plan is the production of single-family homes, a multi-storey wooden building or a housing development project. “Our mission is to accompany our customers competently and in partnership on their way to the project goal. In doing so, we develop innovative solutions together with them that lead them to sustainable success.”