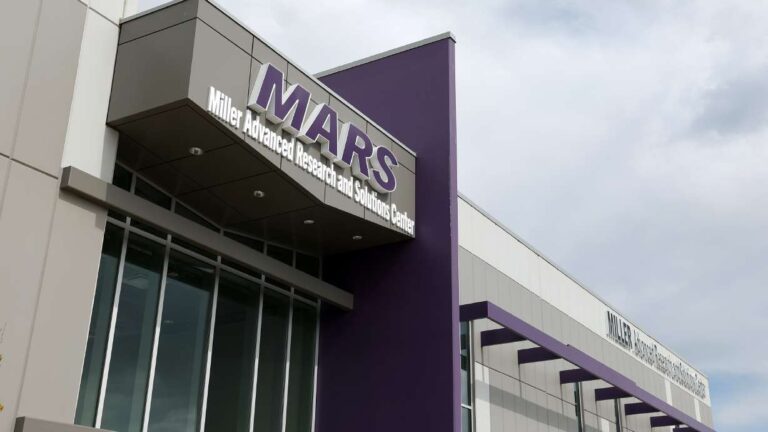
Weber State University is using 3D-printing technology to advance its research on composite materials that support northern Utah’s aerospace and defense ecosystem. (Scott G Winterton, Deseret News)
Estimated read time: 4-5 minutes
OGDEN — The solution for military aircraft and other equipment that needs replacement parts that aren’t in production anymore may come from an unlikely source: 3D printing.
Weber State University is using 3D-printing technology to advance its research on composite materials that support northern Utah’s aerospace and defense ecosystem. It’s all because the university’s Miller Advanced Research and Solutions Center upgraded, installing the Impossible Objects Composite-Based Additive Manufacturing system, or CBAM-2.
CBAM-2 allows the MARS Center to print composite materials that can then be used to design parts for a range of high-tech applications.
“We’re right next to Hill Air Force Base; Northrop Grumman’s right there. We’ve got all these aerospace companies that are out here in Utah,” said Devin Young, a research specialist at WSU who works at the MARS Center. “What we want to be able to do tailor, kind of, our mission. These projects we’re looking at specifically to work with these aerospace companies and help train students for the skills that they’re going to need going forward.”
In Northrop Grumman’s case, this looks like recycling leftover composite materials.
“Composite materials are of high interest to the military, and the ability to 3D-print those parts on demand with CBAM gives us an advantage to participate in more projects and recruit the best talent,” said David Ferro, dean at Weber’s College of Engineering, Applied Science and Technology.
Ferro added that the university has a long history with CBAM technology, but the new system — with better technology and more capabilities than the center’s previous CBAM 3D printer — will serve as a valuable tool for aerospace research in industry and academia.
“We’ve used this technology to print parts for legacy aircraft, aging jets that need replacement parts, or tools that aren’t in production anymore,” Young said. “CBAM makes parts that are lighter and stronger than some of the other methods out there, and it does it faster.”
Young added that the printer is primarily focused on making non-critical, non-structural components of aircraft.
“They’re probably not going to want us to make a mission-critical part where if this fails, your entire aircraft goes down,” Young said.
A recent example of 3D-printed parts from CBAM-2 includes restraining straps that keep first-aid kits secure inside aircraft currently flown by the U.S. Air Force.
“They made them all back in the early ’80s and the ’70s for these aircraft,” Young said.
Eventually, the U.S. Air Force’s first-aid kits got bigger and the previous plastic straps began to crack and break.
Enter the MARS Center and CBAM-2.
It’s kind of new territory, so that’s what’s really exciting about it for me.
–Devin Young, Weber State MARS Center
“We kind of demonstrated that we could make this with CBAM, we could make a stronger part and then you could make a much smaller, limited run,” Young said. “These are critical needs that they have. You have this part that you don’t have any replacements for anymore and the question is, ‘How do you make it?’ because your old methods of making it are 40 years out of date.”
This, Young said, is the beauty of CBAM-2.
He also added that CBAM-2 is extremely proficient at making flat parts. While he acknowledged this might sound strange, there is a need for it, as made apparent in the instance of the restraining straps.
Steve Hoover, Impossible Objects CEO, said the CBAM system’s Carbon Fiber PEEK 3D-printed material achieves excellent mechanical properties and is a cutting-edge alternative for aluminum prototyping, tooling, spares and repairs.
“The MARS Center is at the forefront of aerospace and defense research,” Hoover said. “We’re proud that they’ve selected CBAM technology, and have already engaged in several projects that have exciting potential for the Department of Defense, Department of Energy and other industrial partners.”
Young said that the technology is still so new, it leaves room for exploration to discover where it applies the best.
“I don’t think there’s a manufacturing technology that’s (a) one-size-fits-all solution. I think of it: Instead of being a magic bullet, being more of a quiver of arrows. That’s kind of what’s interesting about this. We’re trying to figure out which applications are best for CBAM versus other technologies,” Young added.
“It’s kind of new territory, so that’s what’s really exciting about it for me.”